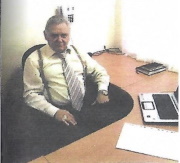
Приведенная работа начиналось еще в России, и было показано, что её реализация может значительно повлиять на состояние стройиндустрии страны. Подготовка песков для бетона позволяет существенно снизить себестоимость и улучшить качество бетонных и железобетонных конструкций - самой массовой продукции строительства.
По существу, исследовательский этап был завершён и подготовлен к внедрению. Из-за репатриации в Израиль работы по этой теме были временно приостановлены: необходимо было прояснить целесообразность их реализации в Израиле.
Была подготовлена к печати монография «Подготовка песков для бетона», где (в том числе) предложено оборудование для получения фракционированных песков, применяемых на предприятиях, изготавливающих бетон и железобетонные конструкции, без их реорганизации.
* * *
Россия- одна из немногих промышленно развитых стран, где при изготовлении бетонов используются заполнители, не подвергавшиеся предварительной подготовке. И если технология получения щебня включает дробление и сортировку, то добытый песок обычно никак не обрабатывается. Исследованиями отечественных и зарубежных ученых показано, что от песка как основного носителя поверхности, гранулометрия которого определяет пустотность заполнителя, главным образом, зависит расход цемента в бетоне. В настоящее время нет единого мнения о том, каковы должны быть критерии качества песка для изготовления бетона. Приемлемыми считаются пески, соответствующие стандарту, а лучшими из них - крупные пески, причём основным критерием, используемым в России для оценки их качества, является модуль крупности.
В то же время различными авторами неоднократно показано, что при одинаковом модуле крупности удельная поверхность песка (никак не менее значимый фактор для оценки его качества чем крупность зерен) может отличаться в 1,5-1,8 раза, и что модуль крупности не может служить надежной оценки качества песка. Тем не менее национальные стандарты ГОСТ 26633-91" Бетоны тяжелые и мелкозернистые. Технические условия " и ГОСТ 8736 -2014 “Пески для строительных работ. Технические условия" на основе этой явно устаревшей малоинформативной характеристики разделяют природные пески на группы, а также предлагают эмпирические зависимости, определяющие рекомендуемые (воспринимаемые производственниками как обязательные) зоны грансостава песков для "высоких" и "низких" марок бетона. Эти рекомендации переходит из стандарта в стандарт, не принимая во внимание исследований последних лет в области заполнителей, а также новые технологии производства бетонов- использование особо жестких бетонных смесей, появление супер- и гиперпластификаторов, эффективных воздухововлекающих добавок, позволяющих использование мелких песков для получения высокопрочных бетонов и др.
За использование необработанных песков приходится платить дважды
Приблизительность критериев, используемых для оценки качества песка, отсутствие привязки его качества к классу бетона и технологическим возможностям формующего оборудования не позволяют оптимизировать состав песка, а применение неподготовленных песков приводит к перерасходу цемента и снижению качества бетона. За использование неподготовленных песков приходится платить дважды: за случайный гранулометрический состав, наличие примесей, а также за нестабильность технологического процесса, в связи с постоянно меняющимися характеристиками материала, в том числе получаемого от одного поставщика, сегрегации песка в процессе погрузочно-разгрузочных операций. Песок имеет также постоянно меняющуюся от замеса к замесу влажность, которую из-за отсутствия надежных экспресс- методов определения её в потоке приходится устанавливать, как правило, органолептически оператором бетоносмесительного узла. Всё это приводит к повышению стоимости бетона из-за увеличения расхода цемента на 15-20 %. В ряде случаев, например, при изготовлении конструкций из песчаного бетона, увеличение расхода цемента по сравнению с использованием песка оптимального грансостава достигает 30%. Перерасход цемента в границах 15-20% при использовании неподготовленных песков в тяжелых бетонах неоднократно подтверждался экспериментальными работами отечественных и зарубежных ученых, а также практикой бетонных работ за рубежом, где это положение отражено в нормативных документах по технологии бетона.
Как известно, в подавляющем большинстве случаев, за рубежом на заводы и стройки поставляется мытые сухие фракционированные пески, что позволяет для каждой марки бетона и удобоукладываемости бетонной смеси (жёсткости, подвижности) готовить оптимальный фракционный состав. Соответственно, бетоносмесительные узлы предприятий снабжены емкостями для хранения отдельных фракций песка и щебня, трактами подачи каждой фракции в смеситель, управляемой компьютером системой дозировки. Причинами, по которым в России не используются фракционированные пески, является, с одной стороны, неготовность предприятий принять, обработать и ввести в бетонную смесь несколько отдельных фракций песка, с другой - неготовность карьеров организовать выпуск фракционированных песков как из-за отсутствия спроса, так и качественного отечественного оборудования для их классификации . По существу, сложилась ситуация замкнутого круга, когда заводы для того чтобы принять отдельные фракции песка нуждаются в реорганизации, а карьероуправления, ГОКи из-за отсутствия заказов не приобретают необходимое оборудование. Проблема усугубляется тем, что приобретение указанного оборудования эффективно только при значительных объемах переработки, что означает поставки фракционированного песка, как минимум, на 3-4 крупных предприятия.
Поиск решения
Когда основные позиции о необходимости и значимости подготовки песков для бетона были сформулированы, стало ясно, что для оценки качества природных песков и схемы их классификации необходима разработка математического аппарата, конечным результатом расчетов с его использованием были бы зависимости (формулы, номограммы), позволяющие установить оптимальный гранулометрический состав песка. Однако при всей очевидности и значимости проблемы даже подходы к ней не были сформулированы, притом что в СССР вопросами качества песков для бетонов занимались выдающиеся ученые Б.Г.Скрамтаев, А.Е.Шейкин, Ю.М.Баженов, И.Н.Ахвердов, В.М.Москвин, И.М.Френкель, С.М.Ицкович. И вот почему - исследования проводились традиционными методами технологов: анализом влияния количества отдельных фракций на конечный результат. Ничего не получалось: слишком многофакторной была задача, причём влияние отдельных факторов на конечный результат было нелинейным. Только в 80 годах сначала в зарубежных, а затем в отечественных публикациях стали появляться статьи о "методе планирования многофакторного эксперимента ", позволяющего учитывать не только влияние отдельных факторов на конечный результат, но и роль каждого фактора. Примерно в то же время в ряде российских НИИ появились ЭВМ, что позволило решать задачи, недоступные для вычисления вручную.
Автором был проведен анализ возможности разработки математического аппарата, позволяющего решение ряда задач: оценить качество природного песка, разработать оптимальный гранулометрический состав песка для конкретного карьера, показать возможность создания " качественного " состава объединением песков двух (и более) карьеров, оценить целесообразность использования укрупнительной добавки и др.
Такой расчётный аппарат- зависимость расхода цемента (именно этот параметр был выбран в качестве критерия оптимизации) от гранулометрии песка был разработан, причём конечный результат устанавливался в зависимости от марки (класса) бетона и удобоукладываемости ( жёсткости, подвижности) бетонной смеси. Аппарат первоначально был разработан для песчаных бетонов как наиболее перспективного направления использования фракционированных песков, а затем откорректирован для тяжёлых бетонов введением в расчётные формулы численных коэффициентов. Экспериментальные работы, включающие испытания бетонных образцов, изготовленных на мытых, фракционированных песках, показали совпадение расчетных и экспериментальных данных в границах 3-5 процентов. Если принять во внимание существующее состояние добычи и переработки песка и на первом этапе внедрения отказаться от принципа получения фракционированного песка для каждого вида тяжелого бетона, а ограничиться усредненными характеристиками, то для большинства выпускаемых бетонов можно указать грансостав песка на конкретном карьере близкий к оптимальному. Получение песков с указанной гранулометрией может быть организовано так, что песок с требуемым соотношением фракций выдается в качестве готового продукта, а "лишние" фракции в разделённом виде накапливается на складах, картах намыва, откуда поставляется потребителям других видов бетонов и растворов, например, для кладочных растворов, отделочных материалов, пено-, газобетона.
Таким образом реальным выходом из создавшегося положения является приготовление фракционированного песка, состоящего из смеси расчетного количества фракций на карьере, и поставка потребителю уже готового к использованию песка. Тогда потребитель (РБК, завод ЖБИ, ДСК) работает в рамках существующего технологического процесса и не нуждается в установке дополнительного оборудования. Разумеется, карьер, который приобрёл, установил оборудование по подготовке песка и организовал технологический процесс, должен компенсировать понесенные затраты увеличением его стоимости. Однако стоимость съэкономленого цемента многократно превышает эти затраты. Кроме того, существенна возможность стабилизации технологического процесса производства бетона на предприятии, а снижение коэффициента вариации прочности бетона станет дополнительным резервом экономии цемента. Классификацию песков целесообразно завершить их обезвоживанием. Снижение влажности поставляемых песков до 3% позволяет полностью избежать смерзаемости, что делает возможным круглогодичную их поставку. Стабилизация расхода воды, привносимой песком в бетонную смесь, позволяет существенно упростить процесс перемешивания, ограничиваясь весовой дозировкой добавочной воды, что, в свою очередь, приводит к дополнительной экономии цемента.
Таким образом в рамках программы подготовки песков для бетонов был разработан расчётный аппарат, позволяющий оценить качество используемого песка по его гранулометрическому составу (рис. 1, рис. 2).
рис. 1. Расход цемента для песчаных бетонов на фракционированных песках (В\Ц=0,3, особо жесткие смеси, трехфакторная модель)
рис. 2. Зависимость расхода цемента от гранулометрии песка (В\Ц=0,3, особо жесткие смеси, пятифакторная модель)
Очевидно, что критерием качества песка должна быть стоимость кубометра бетона на этом песке. Однако в качестве промежуточного достаточного критерия оптимизации может быть принят расход цемента в кубометре бетонной смеси. Поскольку помимо указанных выше характеристик песка расход цемента определяется классом бетона и удобоукладываемостью бетонной смеси, то зависимости, оценивающие качество песка, были построены как функции его гранулометрии для конкретного класса бетона и удобоукладываемости бетонной смеси. Тогда они могут быть представлены в форме квадратичного многочлена, либо симплекс -диаграмм, что позволяет учесть весь комплекс факторов, влияющих на расход цемента.
Разработка математической модели
При разработке математической модели существенно как снижение количества учитываемых факторов, используемых для оценки качества песков, так и возможность надёжного их определения. Например, включение в число факторов удельной поверхности песка значительно упростило бы расчётный аппарат. Однако отсутствие надежной лабораторной базы для её определения и приблизительность этой оценки не позволяют использовать её в качестве фактора. Показано, что в качестве критерия оптимизации следует принять расход цемента в кубометре бетона, а в качестве факторов - результаты рассева песков по стандартам ситам, простую операцию, постоянно выполняемую предприятием.
Ранжированием факторов, оценивающих качество песка для бетонов слитной структуры, установлено, что количество цементного теста не менее чем на 90% определяется гранулометрией песка. Влияние других факторов в подготовленных по указанной схеме песках гораздо менее значимо. Так, влияние коэффициента формы зерен (Кф), зависящего в основном от генезиса песка, было проанализировано и оценивается по расходу цемента максимум в 1,5% при Кф, изменяющимся от 1,0 до 1,5.
Расчётный аппарат, устанавливающий зависимость расхода цемента от класса бетона, удобоукладываемости бетонной смеси и гранулометрии песка, позволяет решить две основные задачи: оценить качество предполагаемого к использованию природного песка и установить гранулометрию оптимального песка, что даёт возможность определить экономию цемента. Наличие расчетного аппарата позволяет также решение ряда промежуточных задач: оптимизировать состав песка поставкой его с двух карьеров, оценить экономическую целесообразность получения фракционированного песка на конкретном карьере.
Порядок подготовки фракционированных песков
Предлагается следующий порядок подготовки фракционированных песков для различных видов бетонов. Исходная песчаная (песчано-гравийная смесь) из карьера доставляется самосвалами и разгружается в приемный бункер. Из бункера дозируемая питателем порция смеси (ПГС) поступает на ленточный конвейер, затем на грохот, выделяющий крупную К- фракцию (-10,0;+1,25). Далее К- фракция поступает на мойку водой, включающей противоморозную добавку. Мытая К- фракция направляется в смеситель.
Фракция (-1,25) с грохота попадает в водный классификатор, где производится её мойка и разделение на среднюю С (-1,25; +0,32) и мелкую М (-0,32; +0,14) фракции. Мытые М и С фракции частично (в соответствии с Техническими условиями на песок конкретного карьера) направляются в смеситель для объединения с К- фракцией . В результате их перемешивания и последующего обезвоживания до влажности 3% образуется «Бетонная» фракция песка, направляемая на крытый склад. Оставшаяся часть С и М фракций раздельно проходят через тонкослойный сгуститель и под названиями - "Растворная "и "Газобетонная" фракции с влажностью 14-15% направляются на открытые склады с фильтрующим основанием. Сливы из мойки, классификатора, обезвоживателя, тонкослойного сгустителя поступают самотеком в пруд- отстойник. Осветленная вода из пруда- отстойника подается насосом для повторного использования (рис.3).
рис.3. Схема подготовки песка для бетона.
Таким образом, установка для подготовки песка предусматривает одновременное безотходное получение мытого фракционированного песка трёх видов: для тяжёлых и песчаных бетонов; для растворов и отделочных материалов; для пено-, газобетона. Все эти пески несмерзающиеся а для тяжёлых и песчаных бетонов- это ещё пески с фиксированной низкой влажностью. Получение чистых песков со стабильной гранулометрией, близкой к оптимальной, и фиксированной влажностью позволяет изготовление бетонных смесей стабильного качества в автоматическом режиме, что приводит к дополнительной экономии цемента из-за низкого коэффициента вариации прочности бетона.
Выводы
Разработка эффективной математической модели позволяет оценить качество песков, используемых при производстве бетона, а также установить их оптимальной гранулометрический состав. В связи с неготовностью заводов ЖБИ и ДСК к приёмке разделённых на фракции песков, предлагается организовать подготовку песка усредненного грансостава, близкого к оптимальному, непосредственно на карьере и использовать его при производстве бетонов основных строительных марок.
Разработана технология и подобрано оборудование для получения на карьере песка, состоящего из смеси требуемого количества фракций. Не вошедшие в объём указанного песка фракции предлагается раздельно разместить в бункерах, на картах намыва для отправки производителям других видов бетонов и растворов.
Использование мытых фракционированных песков позволяет применять их в качестве единственного заполнителя в бетонах без увеличения расхода цемента по сравнению с тяжёлыми бетонами на природном песке. Подготовка мытого фракционированного песка позволяет сократить расход цемента в тяжелом бетоне не менее чем на 60 кг\ куб.м, в песчаном бетоне- на 80 -100кг\ куб.м при одновременном снижении коэффициента вариации прочности и улучшении структурных характеристик материала.